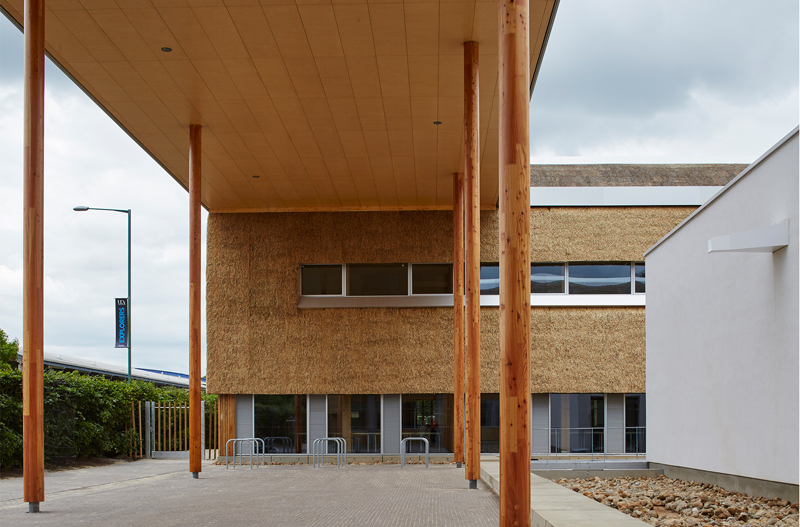
PROJECT INFO
Building type:
Educational
Year:
2015
Project Status:
Built
Gross Area:
3400 Sqm
Certificates:
BREEAM New Construction 2011 (UK) Outstanding
Climatic zone:
Temperate
MY LAST SEEN PROJECTS
PROJECT DESCRIPTION
The Enterprise Centre at The University of East Anglia, dubbed by the press as the UK's greenest building, has been designed and delivered to achieve the Passivhaus standard and a BREEAM outstanding rating. The new university building aims to encourage new sustainable businesses from graduates who emerge from its academic research programme and those involved in activities within the wider Norwich Research Park.
The Enterprise Centre provides space for business support workshops, networking activities, open plan offices, incubation and hatchery space (research and development activities) for new graduate startup companies and other businesses in the Knowledge Economy. The building also provides a base for business support through the University’s Low Carbon MBA and associated graduate development and entrepreneurship programmes operated by the Norwich Business School.
The Concept
The concept comprises a new building and landscape that is an exemplar of low embodied energy and carbon construction technologies, through the use of natural and bio-renewable materials sourced through local supply chains. The Enterprise Centre is a recognised centre of excellence at a European level, providing world-class facilities through its sustainable design and use of materials.
Ben Humphries, Director of Architype and Client Supervisor, said: “With a deep-rooted history and passion for genuinely sustainable design, we have been delighted to be involved in this collaborative, ground-breaking Passivhaus project. Visionary in its brief, we have responded with a design that has pushed at the boundaries of traditional approaches, and with the commitment and dedication of the site team, believe we have achieved a building that sets new benchmarks not only for the university but also the wider construction industry. With an on-going soft landings programme and three years of post-occupancy evaluation to come, we look forward to optimising the building performance for Adapt and the University.”
AWARDS
SUSTAINABILITY FEATURES
Natural ventilation
Shading system
High efficient façade
Photovoltaics
Rainwater harvesting
Water-saving sanitary appliances
Reclaimed materials
Low-emitting materials and finishes
Sustainable sourced timber
Regional materials
Daylighting maximised
SUSTAINABILITY STRATEGY
Why is this building so sustainable? The Enterprise Centre has targeted two of the most rigorous sustainable built environment standards, BREEAM Outstanding and Passivhaus Certification.
To meet the requirements of the brief, we designed the building to meet a 100 year design life, Passivhaus certification and BREEAM Outstanding. The Passivhaus Certification has a very stringent requirement regarding both design and construction. BREEAM Outstanding is made up of 10 categories, which looks at a range of aspects including biodiversity, carbon footprint and water consumption. The building also exceeds the local planning requirement for 10% of the building’s energy to be from renewables through the use of roof mounted PVs.
This is a building which is deeply rooted in its surroundings. The team’s commitment to using indigenous materials, like reed, clay, chalk and hemp, coupled with its focus on utilising local suppliers, contractors and craftspeople, gives the building a real sense of identity and enhances its connection to Norfolk.
The building features a number of ‘world-firsts’; key among these is the use of prefabricated and vertically hung straw thatch panel cassettes, which have been used to clad the building. The straw was sourced locally, to fill timber cassette modules off-site in barns across Norfolk. The prefabricated thatch cassette panels were erected onto the façade of the building, creating a striking, and highly innovative sustainable envelope.
Contributing to the building’s low carbon environmental credentials is the Corsican Pine stud work, locally sourced from Thetford Forest, situated 30 miles from the site. Working closely with Cygnum Timber Frame, The Forestry Commission and Thomson Saw Mill, the design and construction teams worked tirelessly to prove the suitability of the timber, generally not used in construction, for structural elements of the building
Embodied energy has been a major focus at design stage. The Enterprise Centre project is set apart by its rigorous and full lifecycle carbon assessment, from cradle to grave. Overall the embodied carbon of the building has been calculated to be 440kg/CO2/sqm across the 100-year life cycle. This equates to a quarter of the lifetime emissions of a conventionally constructed university building of equal size and scale. Both operational energy and embodied carbon will be monitored and all information will be publicly available.
Other innovations used to achieve this include the use of a recycled sub-base from a local demolition project and a 70% ground granulated blast furnace mix (GGBS) as a cement replacement for the building’s ground floor slab.
On target to achieve Passivhaus with a final airtightness test of 0.21ach@50pascals, the building also features 480m2 solar panels, which are predicted to generate 43.58 MWh in the first year.
A three-year post occupancy and building performance evaluation programme has been implemented with contributions from all team members to assist the occupiers to operate their building optimally and ensure the building performs as designed.
BREEAM
The Enterprise Centre is designed to achieve BREEAM Outstanding, combining best practice across a wide range of sustainability measures.
- Biodiversity features such as insect hotels, bat and bird boxes and the display bed terraces enhance ecological value.
- Site waste management and building recycling nodes.
- Water-saving sanitaryware specification and reusing rainwater for flushing helps with the Water credits.
- Low NOx heating, SUDS and no active mechanical cooling
- Scope for innovation credits through innovative use of materials, BIM and user interaction with the building.
- Good daylighting and ventilation.
- The predicted ‘A’ rated EPC gives the Centre high Energy credits.
- Cycle racks, showers and lockers contribute to the Transport credits.
PASSIVHAUS
The Enterprise Centre is designed to achieve Passivhaus certification, which provides a comfortable internal environment along with radically reduced energy usage.
Key design features considered:
- Triple glazed windows allow beneficial solar gain and good daylighting as well as good insulation levels.
- Mechanical ventilation with heat recovery (MVHR) is used to provide fresh air to all spaces.
- Additional summer ventilation is provided by opening windows and louvres, stack effect and high level exhaust.
- A continuous air tightness layer is detailed around the building.
- Super-thick insulation is wrapped all the way around the building in a ‘duvet’ layer.
GREEN MATERIALS
Many of the materials specified are sustainable and sourced locally;
• 70% GGBS cement
• Recycled sub-base from local demolition
• Insulated slab (Isoquick) - the remnants of this were sent back to the supplier to be recycled
• Timber frame (70% of the stud work was sourced from within 30 miles of the site, corsican pine, Thetford Forest) remainder is Sikta Spruce from elsewhere in the British Isles
• Larch glulams supporting canopy also from Thetford Forest
• Lift shaft made from CLT
• OSB boards domestically sourced
• Local straw applied by local thatchers for the low embodied carbon rainscreen/ cladding
• Byproducts of thatch process used in the production of local wheat beer and flour
• New material trial - external grade MDF for courtyard cladding
• African Iroko cladding, procured form old lab desks in the Universities Chemistry Lab
• Recycled reception desk- the Norman Foster design from the Sainsbury Centre
• Timber slat low grade soft wood on some ceiling areas
• Wood wool acoustic sound boards
• New material trial - spray on cellulose (acoustic finishing treatment) made from 85% recycled paper
• Recycled car tyre flooring
• Solvent free natural based paints and oil finishes
• Pods are distinguished by a range of interesting and ecological wall coverings including Hemp fabric, Nettle Fabric, earth board and locally sourced reed boards
• Long lasting ground floor finish - diamond ground concrete (low maintenance will last building lifespan)
first floor finished in linoleum (linseed and hessian matting on recycled glass screed)
ENERGY DATA
Energy consumption:
N/A (N/A )
Consumption type:
Simulated
Annual carbon footprint:
440.00 KgCO2m² (4736.121 KgCO2/ft²)
Climate zone:
Temperate
Min. temperature =
N/A
Max temperature =
N/A
RH =
N/A
CLIENT
Client:
Adapt Low Carbon / UEA
DESIGNERS
Architect:
Architect:
CONSULTANTS
Acoustical consultant:
BDP
Building services engineer:
BDP
Environmental consultant:
BDP
Green certification consultant:
BDP
Specialist consultant:
Churchman Landscape Architects
Structural Engineer:
BDP
CONTRACTORS
Contractor:
Morgan Sindall
OTHER PROJECTS BY TEAM
SIMILAR PROJECTS
Chia, Cundinamarca, Colombia | 2013
49 Bow Rd, London E3 2AD, UK | 2013
Sydney NSW, Australia | 2015
Edinburgh Centre for Carbon Innovation, Edinburgh EH8, UK | 2013
Via Renzo Ildebrando Bocchi, 33, 43126 Parma PR, Italia | 2012
Heidelberglaan 8, 3584 CS Utrecht, Netherlands | 2015
Corso Venezia, 37047 San Bonifacio VR, Italy | 2012
Via Giuseppe Mazzini, 37047 San Bonifacio VR, Italia | 2012